Magnetic Particle Inspection MPI57
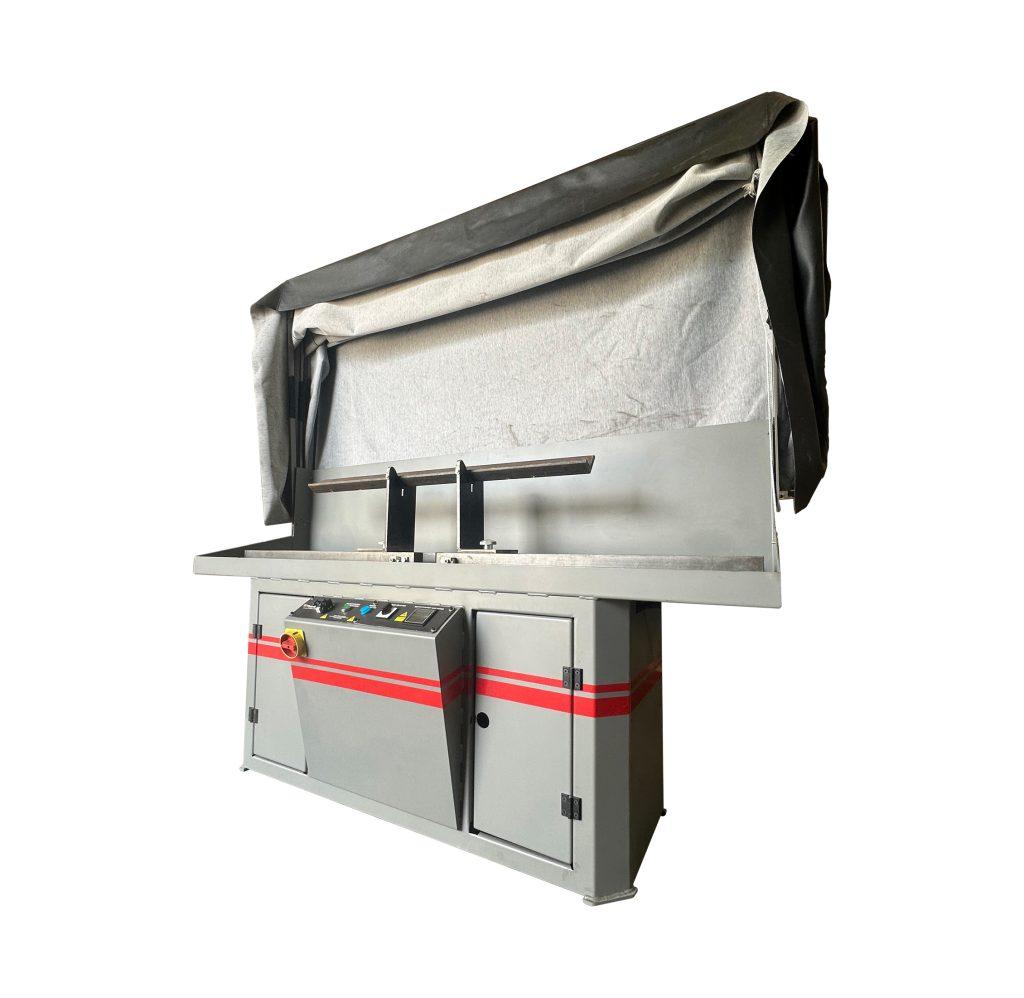
Magnetic Particle Inspection (MPI) is a non-destructive testing (NDT) method used to detect surface and slightly subsurface discontinuities in ferromagnetic materials. This technique is widely used in various industries, including automotive, aerospace, and manufacturing, to ensure the integrity and reliability of critical components.
Magnetic Particle Inspection Equipment is designed to detect exterior cracks or flaws in ferrous metal.
Magnetic Particle Inspection is a crucial non-destructive testing method for detecting surface and near-surface defects in ferromagnetic materials. Its high sensitivity, efficiency, versatility, and non-destructive nature make it an invaluable tool in various industries to ensure the integrity and reliability of critical components.
Request A Quote
Product Information
Operations
The MPI57 is an A.C. machine. Unlike D.C. units, parts will not retain residual magnetism which is critical to some parts such as crankshafts. A.C. machines do not require reversing polarity to demagnetize, thus less time is spent in inspection. The MPI57 can, however be used to demagnetized parts that are already magnetized (HOT).
The MPI57 is versatile, permitting inspection of a wide variety of parts such as crankshafts, connecting rods, camshafts, gears, struts, spindles, bolts, and other types of ferrous metal parts.
Specifications
Electric Magnetothermic Protection: Automatic
Length: 63” (1600 mm)
Width: 24” (610 mm)
Height: 52” (1300 mm)
Length 63” (1600 mm)
Width: 24” (610 mm)
Height: 83” (2100 mm)
Features
Standard Tooling
– UV-rays lamp for inspection
– Plastic sprayer for spraying the detecting fluid
– Foot lever for operation of magnetoscope with
busy hands
– Pair of unipolar cables with insulated grips
– Splash-guard